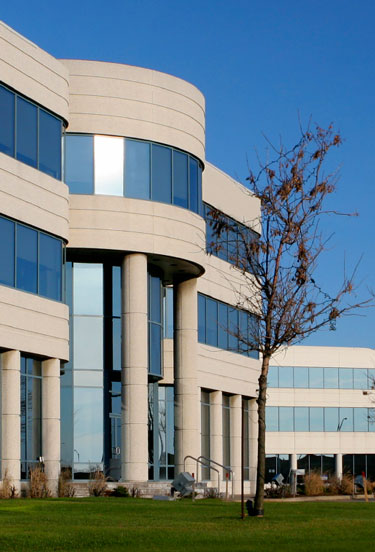
Virtual Environmental Manager - Compliance Center
In order to ensure continued facility compliance with regulatory requirements, it is necessary to understand how these regulation apply to a facility. Here are some tips to help avoid non-compliance situations.
Local and state air pollution control agencies regulate air pollution from manufacturing facilities through permit programs. Activities that can trigger permit requirements should never occur prior to obtaining the permit approval. Any activities should be cleared through the air pollution control agency prior to conducting such activities.
Facilities can hold off any potential non-compliance issues by understanding permit conditions. Key questions needed to be considered in order to ensure that the permit is interpreted properly:
- Can my facility meet all of the conditions under normal operating situations?
- Are future production increases going to cause my facility to fall out of compliance with any of the conditions?
- What is my plan for demonstrating compliance with permit conditions?
Many times, a facility will underestimate the quantity of raw material usage, hours of operations, or its actual emission rate. Permit conditions should be developed to accomodate a wide range of operating conditions and scenarios in order to avoid non-compliance with the permit.
Periodically, a local air pollution agency's inspector will conduct a facility inspection. The facility's operations will be thoroughly examined in order to verify compliance with all applicable air quality regulations and permit conditions.
Facility records are often reviewed during these inspections, so all collected annual data that documents air emissions are required to be presented. These inspections also serve as a mechanism for the facility to have any questions answered, information requested, as well as learn about upcoming regulatory changes.
A facility should develop and implement a facility-wide compliance plan to ensure continued compliance with all applicable air quality regulations and permit conditions. The compliance plan should cover at a minimum:
- Periodic inspection schedules and records of all equipment and control equipment.
- Monitoring and recording schedules and procedures for equipment and control equipment performance.
- Prompt repair schedules and procedures of any defective equipment or control equipment.
- Procedures for the facility's start up, shut down, and normal operations.
- Control measures to ensure compliance
- Record of all actions required by the plan, including corrective actions.
Copyright 2007, Entech Consulting Group |